HD Series
Multi component injection molding machine(160T-850T)
FLEXIBLE MULTI-COMPONENTS CREATE MORE VALUE
Manual download
- introduction
- Machine
- System
- other
INTRODUCTION
HD Series
-
P位/POSITION
2ndinjection unit horizontal and parallel to zhe first
Shortest center space of mould is 200mm
-
L位/POSITION
2ndinjection unit horizontal on the back of machine
Ideal for larger shot weight
-
V位/POSITION
2nd injection unit at vertical angle of the mould
Ideal for smaller shot weight and space-saving
-
W位/POSITION
2nd injection unit at 45°angle above the horizontal unit
Ideal for smaller shot weight, space-saving, lower height required
-
M位/POSITION
2nd injection unit in the back of moving platen
Ideal for injection molding of large parts,Swivel platen shares mould weight equally
-
TTURNTABLE TECHNOLOGY
Two component parts (two stations in the mould), the perform is moved to the 2nd injection position by a 180°rotation through high precision turntable. In the case of three or four components (three or four stations), the angle of rotation is 120°or 90°.
-
SSWIVEL PLATENTECHNOLOGY
The swivel platen is installed on the vertical axis of the machine, between the fixed platen and the moving platen. The preform is moved by rotating the vertical centeral axis of the swivel platen. It is available with DP two platen clamping structure, which is especially suitable forlarge-scale multi-components injection molding. The swivel platen shares the weight of the mould and effectively reduce the clamping force requirements of the part, so that customers can choose smaller tonnage injection molding machines,
-
IINDEX PLATE
The center of the moving platen is equipped with a rotating structure that can rotate 180°, which drives the mould to axial motion and moves the prelorm to the 2nd station.
-
BBI-INJECTION
Bi-njection is the injection of the same raw materials of two colors into the cavity through two independent gates. No accurate parting line on the product.
-
CCORE BACK
In the core back process, the programmable core puller is used to control the movement of the mould slider to inject the 2nd component. There is regular parting line on the product.
FEATUREES
HD Series FEATUREES
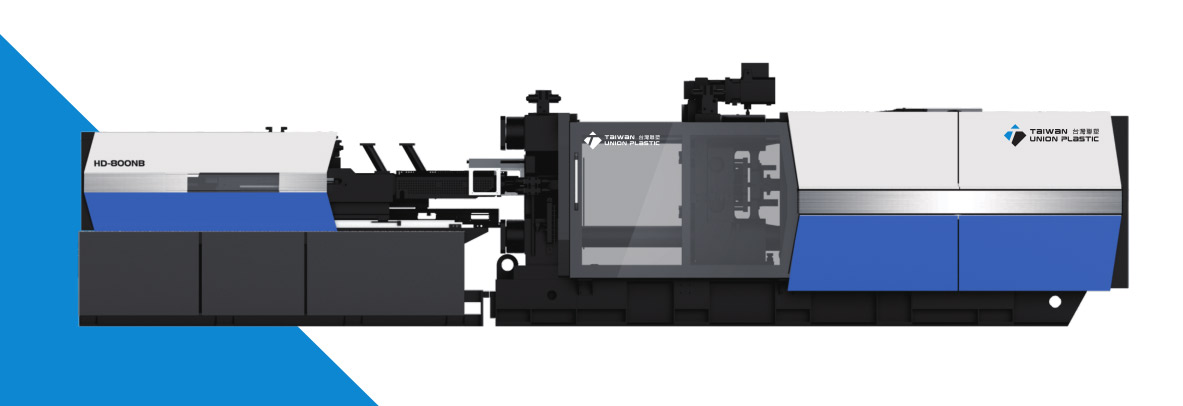
-
01
HIGH SPEED AND PRECISION TURNTABLE
The high-precision turntable is controlled by servo motor, which is fast and stable with high load intensity. The controller monitors the turntable position deviation in real time through the rotary encoder
LARGE SPACE FOR MOULD
Super wide tie bar design, suitable for more mould types, therebyreducing procurement costs
-
02
PATENTED TURNTABLE STOPPER
Completely keep turntable from dropping.Adopted integrated base, simplified structure and higher reliability
-
03
SLIDING FOOT
Lengthened and widened sliding foot ofmoving platen optimizes platen parallelism even with heavy mould
-
04
HIGH PRECISION LINEAR GUIDE ON INJECTION UNIT
Injection and plasticizing syster adopts linear guide with high precision.high rigidity and low coefficient of friction
-
05
UNIQUE EJECTION STRUCTURE (OPTIONAL)
Able to work as single component machine with 3 ejection cylinders design
-
06
HIGH EFFICIENT HYDRAULIC SYSTEM
Equipped with independent hydraulic servo system. Reasonable oil circuit layout and low pressure loss
-
07
FLEXIBLE COMBINATIONS OF MULTI-COMPONENTS
Meets customized needs of parts in diversilication and individuation
CONTROL SYSTEM
HD Series CONTROL SYSTEM
CONTROL SYSTEM
Friendly human-machine interface and high-precision control system, convenient operation, stable running and excellent extensibility. Able to equip with MES system to realize network management of production workshop.
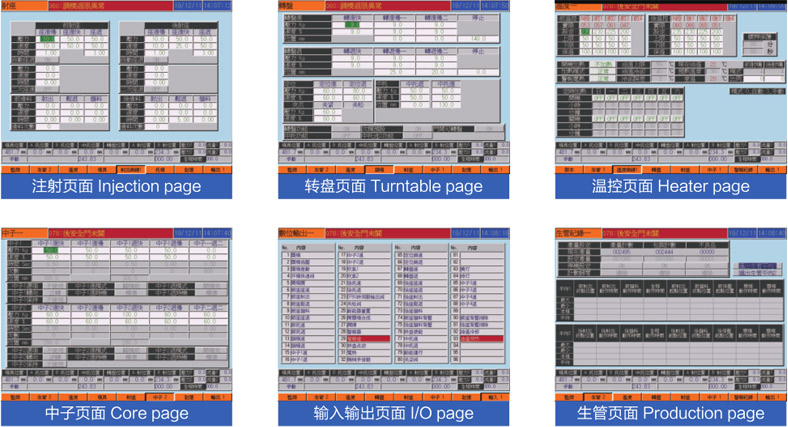
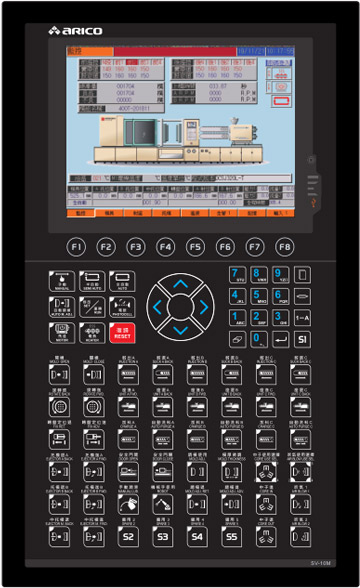
OTHERS
HD Series OTHERS
-
Product case
In this day, the consumer product styles are changing frequently, they require attractive appear-ance and exquisite design, but also quickly to meet market demand. Designers will use differentmaterials in different parts according to different uses of consumer products to meet the needsof specific environments, to achieve the purpose of extending product life, increasing aestheticsand practicality. This practical design requirement will undoubtedly lead to complicated produc-tion technology. The multi-color (multi-component) injection molding process is born out of thistrend.
Multi-color (multi-component) application areas cover many industries such as automobiles,household, electronics and home appliances, construction, packaging and medical equipment.With the advancement of technology, the application of multi-color (multi-component) injectionmolding technology has become increasingly widespread.